Global service: MESSRING provides customers with maintenance teams that ensure uninterrupted availability of crash test facilities and offer technical assistance when it comes to carrying out unique test runs.
The automotive industry is changing radically, increasing pressure on operators of crash test facilities all over the world. The search for new mobility and drive concepts, the development of driver assistance systems, and changing test regulations all increase the demand for and complexity of test runs, particularly for OEMs and their suppliers. Whether it’s due to unnecessarily long reconfigurations or (even worse) unforeseen repairs or maintenance, downtime is more expensive than ever. MESSRING can help by offering its customers expanded services: Upon request, the global market leader in crash test facilities and their components can provide its own service teams to look after customer facilities and ensure uninterrupted availability of the crash test facility. What’s so special about these teams is that they work independently, but are seamlessly integrated into operations and always on-site during operating times. They not only assume responsibility for continuous facility maintenance and servicing, but also support the team of operators with their technical know-how – and can even help conduct new or rarely used test runs. This not only increases testing efficiency, but also minimizes the downtime following system failures or unplanned repairs.
“OEMs and automotive suppliers are increasing their focus on their core area of expertise,” says Dierk Arp, Managing Director of MESSRING. “And that clearly doesn’t include repairing and maintaining third-party equipment.” As a result, three German premium-class vehicle manufacturers have opted for maintenance contracts with MESSRING for their crash test facilities, enabling comprehensive support on-site. MESSRING provides each of these customers with their own individually structured team of technicians that work independently to ensure seamless operation and the desired facility availability.
Because the MESSRING technicians are involved in operation of the crash test facility and on-site every day, they can plan upcoming work in such a way that it doesn’t interfere with testing at any time. Cleaning, replacement of wear parts, and calibration of measurement instruments are all coordinated with testing to prevent unnecessary downtime. The facility is ready whenever they need it. “It’s a classic win–win situation,” says Arp. “Our customers rest assured that they can optimally use their system at any time, and we as a manufacturer of crash test facilities are given user-specific, practical feedback, which can help us further enhance facilities and parts.”
In addition to servicing, maintenance, and repairs, the MESSRING technicians increasingly help carry out test runs that are not part of the standard program. This includes providing the team of operators with technical support, for example, when data capture is not possible with the existing equipment and simple, practical solutions need to be developed. But it also encompasses advice on component preparation for new test runs, for instance, when programming new test procedures.
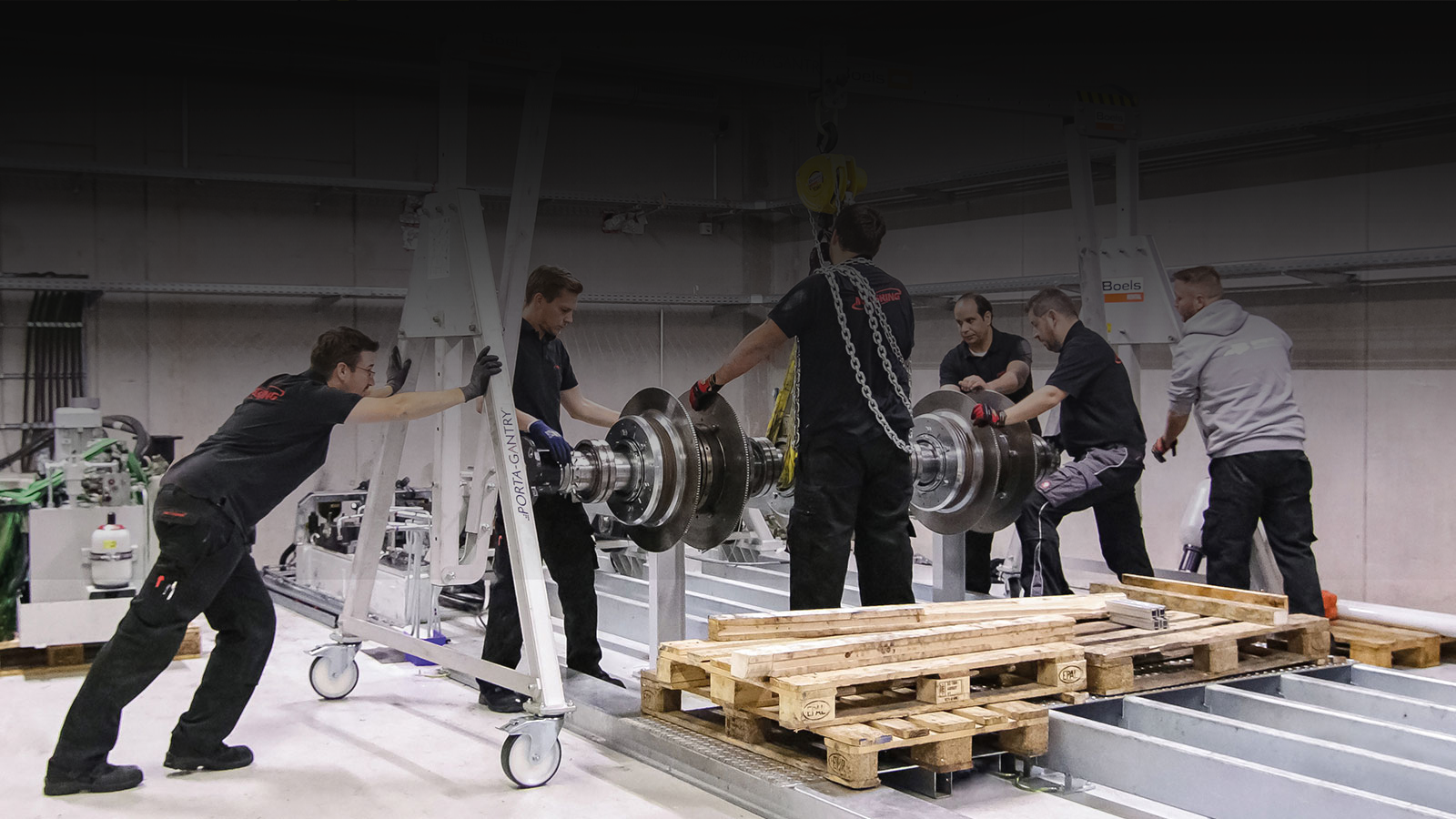
“This flexibility and assurance that our teams offer on-site is becoming more and more important to our customers,” explains Arp.
The service team’s structure and equipment can be adapted to the customer’s specific requirements and integrated into the company’s work structure. A separate ticket system can also be set up. Depending on the conditions on-site, MESSRING employees can have their own offices directly at the test site or in close proximity. The team’s technical equipment ranges from simple standard equipment to fully equipped workshops that measure hundreds of square meters and have their own test rigs, calibration instruments, milling machines, and a whole lot more.
Regardless of the equipment and selected service team structure, there’s one benefit you can always count on: Because it’s not a temporary team with members coming and going, technicians generally only need to undergo safety testing and accreditation once. This in turn eliminates any time lost due to additional bureaucracy and maintains the obligation of confidentiality. A good example of the service that can now be used all over the world is a collaboration model that MESSRING has successfully implemented for a vehicle manufacturer in southern Germany for more than 25 years. Four mechatronic technicians with special in-house training provided by MESSRING are always at the facility during operating times and are responsible for service and ensuring availability. According to Arp, the success speaks for itself: “In the many years that the maintenance contract has existed, there hasn’t practically been a single day when the crash test facility operations had to be suspended.”