Die Anforderungen an Crashtest-Anlagen werden immer komplexer und vielfältiger.
Emissionsfreie Antriebe, aktive Sicherheitssysteme, vernetzte Mobilität bis hin zum autonomen Fahren – die Automobilindustrie bereitet sich auf einen gewaltigen Innovationssprung vor. Entsprechend groß sind die Anforderungen an neue Crashtest-Anlagen und Testsysteme. Hier muss eine Zukunft vorausgeplant werden, von der man bislang allenfalls erahnen kann, wie sie einmal aussehen wird. Eine enorme Herausforderung für alle, die automobile Testplattformen für die kommenden Jahre zukunftsfähig konzipieren und realisieren wollen.
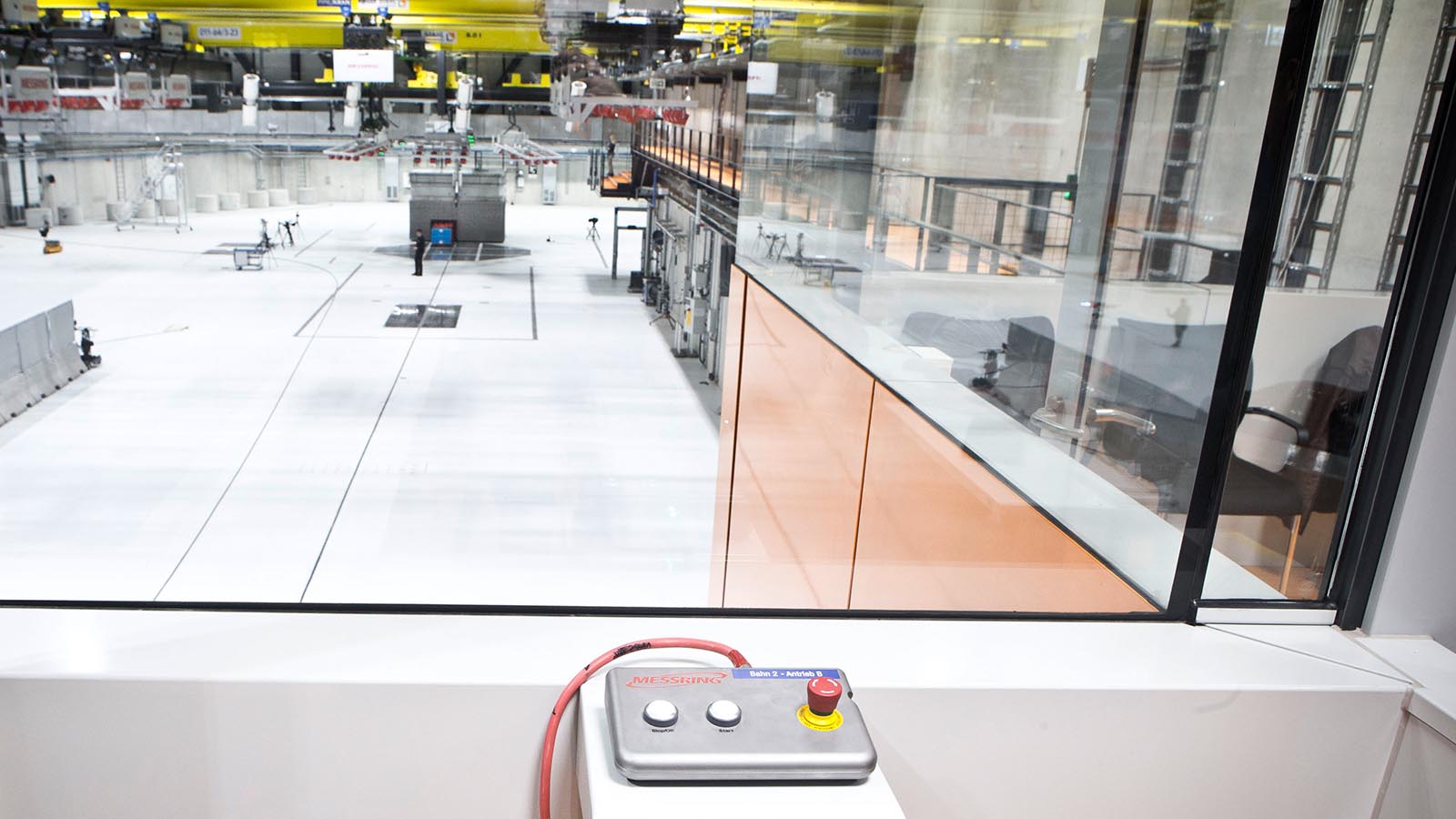
Wenn Arp auf die letzten Jahre von MESSRING zurückblickt, dann fällt ihm eines auf: “Wir sind zunehmend als Entwickler und Problemlöser gefragt.” Längst beschäftigt sich MESSRING nicht mehr allein mit dem Bau von Crashtest-Anlagen oder deren Komponenten in aller Welt, sondern auch mit hochspeziellen Fragestellungen zur allgemeinen Verkehrssicherheit.
Bestes Beispiel: Das Ende 2016 in Betrieb genommene Technologiezentrum Fahrzeugsicherheit (TFS) von Mercedes-Benz in Sindelfingen, an dessen Planung, Entwicklung und Realisierung MESSRING maßgeblich beteiligt war. Das TFS bietet Sicherheitsingenieuren völlig neuartige Testmöglichkeiten, etwa im Hinblick auf Car-to-Car-Versuche mit selbstfahrenden und gezogenen Fahrzeugen, die Auslegung von Assistenzsystemen oder Fahrzeugkonzepte mit alternativen Antrieben. Auf einer säulenfreien, 90 mal 90 Meter großen und überdachten Fläche können autonom fahrende und gezogene Fahrzeuge künftig für Crashversuche synchronisiert werden. Ausweich- und Bremsmanöver durch Fahrerassistenzsysteme in der Pre-Crash-Phase lassen sich somit in Tests integrieren – und das nicht nur mit Fahrzeugattrappen, sondern erstmals auch mit Autos, die durch die Anlage bewegt werden. Fahrerassistenzsysteme können damit gezielt und kontrolliert an ihre Grenzen gebracht werden. Die für Fahrzeugentwickler so wichtige Frage, wie effektiv Assistenzsysteme arbeiten und wie sich Karosserie und Insassen vor und nach dem eigentlichen Unfall bewegen, kann insgesamt noch genauer untersucht werden.
Bis zu 900 Tests und 1.700 Schlittenversuche sollen im TFS pro Jahr gefahren werden. Um diese einzigartige Infrastruktur zu schaffen, war viel Entwicklungsarbeit nötig, auch im Hause MESSRING.
Anlagensteuerung
Das TFS verfügt über mehrere Crashbereiche, vier davon können bei Bedarf gleichzeitig und unabhängig voneinander betrieben und gesteuert werden. Rund 70 verschiedene Crashtest-Konfigurationen für PKW und LKW sind möglich. Allein der überdachte Teil der Crashhalle ist größer als ein internationaler Fußballplatz. Die längste Crashbahn misst zudem deutlich über 200 m. Die Abmessungen und die schier unübersehbare Zahl der Subsysteme und Peripheriegeräte sprengen damit alle bisher bekannten Dimensionen.
Unvermeidbare Konsequenz: Lineare Bus-Systeme zur Verteilung von Takt- und Triggersignalen, wie sie in der Steuerung moderner Crashtest-Anlagen bislang zum Einsatz kommen, stoßen hinsichtlich Präzision, Handling und Ausfallsicherheit an ihre Grenzen. Ein neuer Lösungsansatz zur Anlagensteuerung und insbesondere zur Verteilung von Takt und Trigger musste also gefunden werden. MESSRING lieferte prompt – und entwickelte mit M=SYNC erstmals eine hochfrequente digitale Kommunikationsinfrastruktur, welche Datenpakete störsicher und mit Lichtgeschwindigkeit bis in die entferntesten Bereiche der gewaltigen und hoch komplexen Anlage schickt. Anstelle des linearen Bus-Systems tritt nun ein nahezu beliebig erweiterbares Netz mit Triggerboxen, die über mehrere Kilometer Glasfaserkabel miteinander verbunden sind. Alle Geräte erhalten über das globale System ein identisches Triggersignal sowie ihre individuellen Taktraten. Für nicht weniger als 24 verschiedene Szenarien zur Konfiguration der Gesamtanlage programmierte MESSRING zudem eigene Kommunikationsprotokolle. Sie können auf Knopfdruck abgerufen werden und stellen sicher, dass einzelne Crashbereiche ohne Zeitverlust auch individuell und isoliert genutzt werden können. Eine wichtige Voraussetzung für den effizienten Betrieb der Anlage.
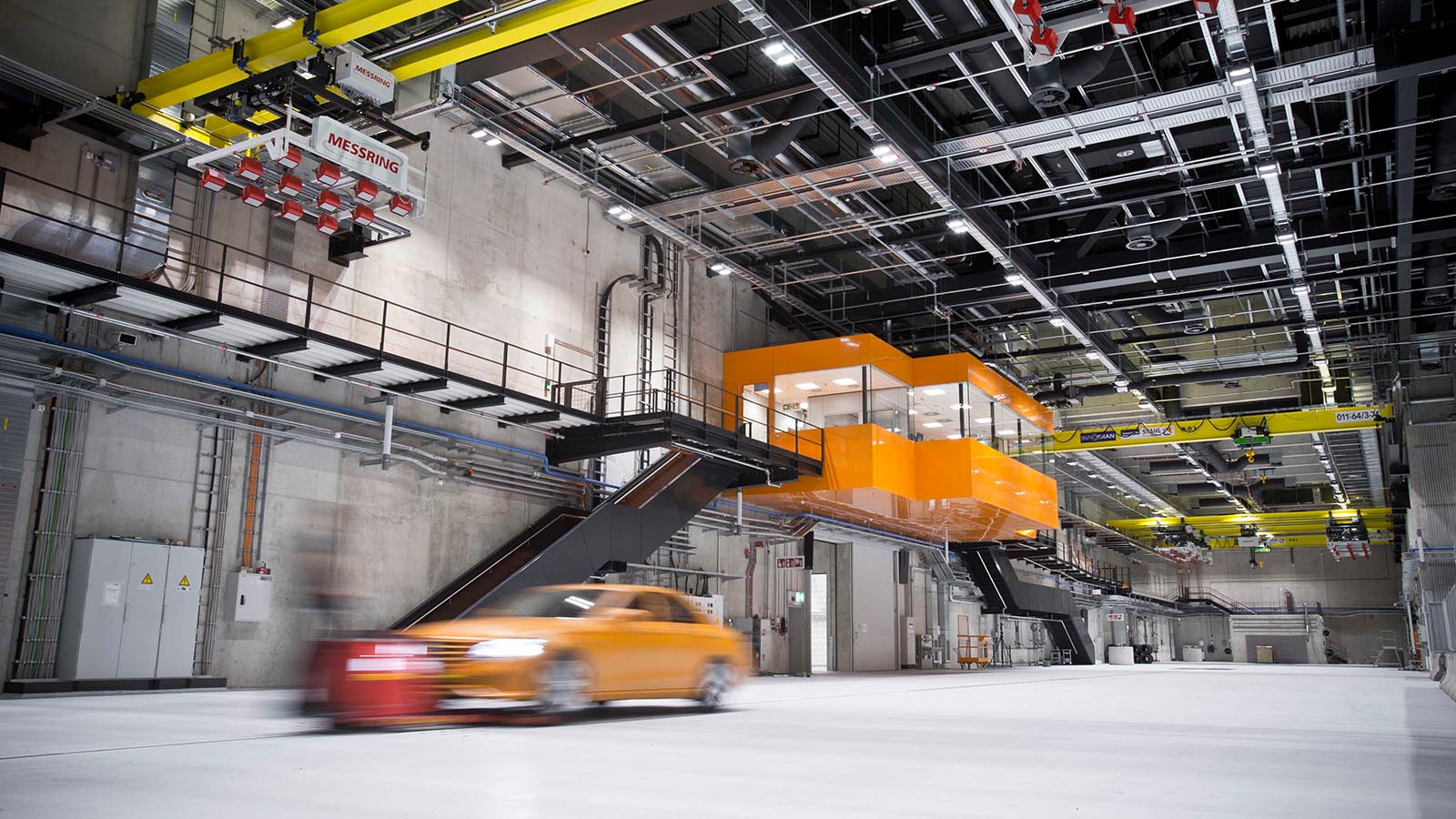
Spezialisten aus unterschiedlichen Disziplinen leisteten die Entwicklungsarbeit für M=SYNC. Elektroingenieure, Mechatroniker und Softwareentwickler von MESSRING erstellten im Rahmen der Nullserie zunächst nicht weniger als fünf Prototypen, um die Infrastruktur ausgiebigen Tests unterziehen zu können. Mehr als 6.700 Projektstunden waren nötig, bis aus der ersten Idee ein fertiges Produkt wurde. Das geballte Knowhow des interdisziplinär arbeitenden Teams führte schließlich zum Erfolg.
Mobiler Crashblock
Auch bei der Entwicklung des weltweit ersten uneingeschränkt mobilen Crashblocks konnte MESSRING seine Stärken ausspielen und sich als Sparringspartner und Ideenentwickler profilieren. Vorgabe von Mercedes-Benz war es, einen selbstfahrenden Block zu entwickeln, der sich trotz seiner 110 Tonnen Gewicht völlig frei, sicher und möglichst unkompliziert innerhalb der Crashhalle navigieren lässt. Keine Kabelstränge sollten die Wege blockieren. Keine festen Routen sollten vorgegeben werden. Stattdessen: Maximale Flexibilität und ein möglichst einfaches Handling.
MESSRING stellte hierfür ein interdisziplinäres Entwicklungsteam zusammen, das das Konzept des mobilen Blocks aus der bestehenden MESSRING-Produktpalette von Grund auf überplante. Der Koloss erhielt ein komplett überarbeitetes hydraulisches Fahrwerk, ein neues Akkusystem und neue Sensortechnik. Die Verankerung und Verriegelung des Blocks im Boden wurde überarbeitet. Schließlich integrierten Experten ein lasergesteuertes Navigationssystem zur besseren Orientierung in der Halle.
Rund 20 Experten aus unterschiedlichen Bereichen wie Konstruktion, Automation, Programmierung, Lasertechnik, Mechanik und Elektrotechnik arbeiteten teilweise gleichzeitig an dem Projekt. Sie schufen einen autark fahrenden Block, der binnen weniger Minuten an jeden beliebigen Ort in der Halle gesteuert werden kann. Analog zur Standardausführung sind die vier Aufprallseiten mit unterschiedlichen Barrieren vorkonfiguriert. Durch einfaches Drehen des Blocks können somit unterschiedliche Testszenarien vorbereitet werden.